Catalytic Oxidation
What is it?
Catalytic oxidisers operate in a very similar way to thermal oxidisers, with the main difference being that the gas, after passing through the flame area, passes through a catalyst bed. The catalyst has the effect of increasing the oxidation reaction rate, enabling conversion at lower reaction temperatures than in thermal oxidation units. Catalysts, therefore, also allow smaller oxidisers to be used. The principle is illustrated in Figure 1.
The waste gas is heated by auxiliary burners to approximately 300–500 °C before entering the catalyst bed. The maximum design waste gas temperature of the catalyst is typically 500–700 °C. There are low-temperature catalysts that work at temperatures of 200–250 °C.
The method of contacting the gas stream with the catalyst serves to distinguish catalytic oxidation systems. Both fixed-bed and fluidised-bed systems are used.
Catalysts for VOC oxidation are typically either precious metals, such as platinum, palladium and rhodium, supported on ceramic or metal, or base metals supported on ceramic pellets, single or mixed metal oxides, often supported by a mechanically strong carrier, such as oxides of copper, chromium, manganese, nickel, cobalt, etc. Platinum-based catalysts are active for the oxidation of sulphur-containing VOCs, whereas they are rapidly deactivated by the presence of chlorine.
The waste gas is heated by auxiliary burners to approximately 300–500 °C before entering the catalyst bed. The maximum design waste gas temperature of the catalyst is typically 500–700 °C. There are low-temperature catalysts that work at temperatures of 200–250 °C.
The method of contacting the gas stream with the catalyst serves to distinguish catalytic oxidation systems. Both fixed-bed and fluidised-bed systems are used.
Catalysts for VOC oxidation are typically either precious metals, such as platinum, palladium and rhodium, supported on ceramic or metal, or base metals supported on ceramic pellets, single or mixed metal oxides, often supported by a mechanically strong carrier, such as oxides of copper, chromium, manganese, nickel, cobalt, etc. Platinum-based catalysts are active for the oxidation of sulphur-containing VOCs, whereas they are rapidly deactivated by the presence of chlorine.
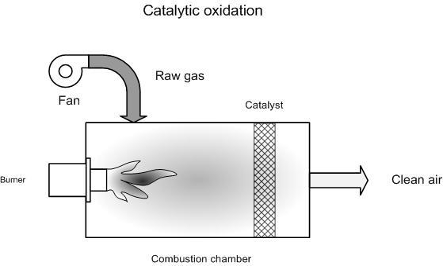
Figure 1. Principle of catalytic oxidation
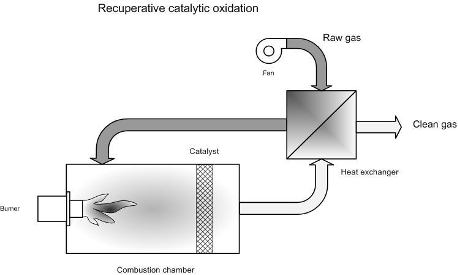
Figure 2. Principle of catalytic oxidation with heat recovery
The presence of catalyst poisons or masking (blinding) agents in the waste gas stream, such as particulates or reactive chemicals, can have a significant impact on the working life of the catalyst. Poisoning by blinding can be reversible, e.g. coating of the catalyst surface by oils or fats reduces its efficiency but the coating can be burnt off by raising the temperature. However, if certain chemicals are present, the poisoning of the catalyst becomes irreversible.
As with thermal oxidation, straight catalytic oxidisers, regenerative catalytic oxidisers and recuperative catalytic oxidisers are used.
Normal operating conditions for catalytic oxidisers include:
As with thermal oxidation, straight catalytic oxidisers, regenerative catalytic oxidisers and recuperative catalytic oxidisers are used.
Normal operating conditions for catalytic oxidisers include:
- natural gas as the preferred fuel (when additional fuel is needed);
- a distributed burner as a suitable burner;
- chambers constructed of stainless steel or carbon steel;
- a burner section with a sufficient length to provide an even flow and temperature distribution across the catalyst surface;
- flat flow profile across the catalyst surface;
- waste gas moving through the catalyst bed in 'plug flow' with minimum back mixing;
- a typical residence time of 0.3–0.5 seconds.
Design, maintenance and efficiency
The catalytic oxidation should be designed in such a way as to facilitate the removal of the catalyst for cleaning or replacement purposes.
Catalytic oxidisers should be inspected regularly, and, if necessary, cleaned to maintain good performance and efficiency. When excess depositions occur, preventive actions should be taken by (partially) cleaning the incoming gas before it enters the oxidiser.
The catalyst bed temperature, the pressure drop across the catalyst bed, the combustion temperature and the carbon monoxide and oxygen content of the effluent gas stream should be monitored to maintain optimal combustion conditions.
Catalytic oxidation is most suited to systems with lower waste gas volumes, when there is little variation in the type and concentration of VOCs, and where catalyst poisons or other fouling contaminants are not present.
The catalyst bed temperature, the pressure drop across the catalyst bed, the combustion temperature and the carbon monoxide and oxygen content of the effluent gas stream should be monitored to maintain optimal combustion conditions.
Catalytic oxidation is most suited to systems with lower waste gas volumes, when there is little variation in the type and concentration of VOCs, and where catalyst poisons or other fouling contaminants are not present.
Applicability
Catalytic oxidation is mainly used for the removal of VOC from solvent evaporation. Implementation examples are:
Table 1 shows application limits and restrictions associated with catalytic oxidation (adapted from EIPPCB, 2016, Table 3.209).
Table 1. Application limits and restrictions associated with catalytic oxidation.
- Bulk-loading fuel stations;
- Production of organic chemicals;
- Production of rubber and polymers;
- Resin production;
- Application and drying of solvent-laden coatings.
Table 1 shows application limits and restrictions associated with catalytic oxidation (adapted from EIPPCB, 2016, Table 3.209).
Table 1. Application limits and restrictions associated with catalytic oxidation.
Issue | Limits/ Restrictions |
---|---|
Gas flow (Nm3/h) | 1200-90000 (straight and regenerative oxidiser) 90-90000 (recuperative thermal oxidiser) |
Temperature (°C) | 300-500 before the catalyst 500-700 after catalyst |
Pressure (MPa) | Atmospheric |
Pressure drop (mbar) | 10 - 50 |
Particulate content (Nm3/h) | <3 |
Residence time(s) | 0.3 - 0.5 (dependent on catalyst bed volume) |